Activated Carbon Basics
What is Activated Carbon?
Activated carbon is a carbonaceous, highly porous adsorptive medium that has a complex structure composed primarily of carbon atoms. The networks of pores in activated carbons are channels created within a rigid skeleton of disordered layers of carbon atoms, linked together by chemical bonds, stacked unevenly, creating a highly porous structure of nooks, crannies, cracks and crevices between the carbon layers.
Activated carbons are manufactured from coconut shell, peat, hard and soft wood, lignite coal, bituminous coal, olive pits and various carbonaceous specialty materials. Chemical activation or High Temperature Steam Activation mechanisms are used in the production of activated carbons from these raw materials.
The intrinsic pore network in the lattice structure of activated carbons allows the removal of impurities from gaseous and liquid media through a mechanism referred to as adsorption. This is the key to the performance of activated carbon.
Adsorption
Adsorption is the attachment or adhesion of atoms, ions and molecules (adsorbates) from a gaseous, liquid or solution medium onto the surface of an adsorbent – activated carbon. The porosity of activated carbons offers a vast surface on which this adsorption can take place. Adsorption occurs in pores slightly larger than the molecules that are being adsorbed, which is why it is very important to match the molecule you are trying to adsorb with the pore size of the activated carbon. These molecules are then trapped within the carbon’s internal pore structure by Van Der Waals Forces or other bonds of attraction and accumulate onto a solid surface.
Typically 1 m3 of Activated Carbon with 0.3m3 of internal pores can adsorb 30m3 or more of a gas, even if present in low concentrations in a carrier.
Different Types of Activated Carbon
Activated carbon is mainly available in three forms or shapes: powder, granular and extruded. And each form is available in many sizes. Based upon the application and requirements, a specific form and size are recommended.
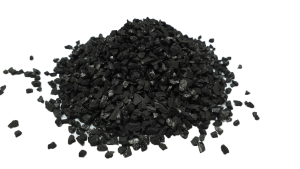
Granular Activated Carbon (GAC)
GAC are irregular shaped particles formed by milling and sieving. These products range from the sizes 0.2mm to 5 mm. They have the advantages of being harder and longer lasting than powdered activated carbons, clean to handle, purify large volumes of gas or liquids of a consistent quality, and can be reactivated and reused many times. GAC are used in both liquid and gas phase applications and in both fixed and moving systems.
In liquid phase uses, granular activated carbon is packed in columns and towers through which liquids flows. GAC are used where there is a single product to be refined or produced continuously in large quantities. In gas phase applications GACs have the advantage of having sufficient flow with an acceptable pressure drop through the carbon bed.
In addition, granular activated carbons are nearly always regenerated and reused, The period between reactivation varies significantly but is on average 18 months. Loss of material during reactivation ranges from 5% to 15%.
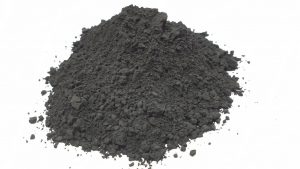
Powdered Activated Carbon (PAC)
PACs generally have a particle size distribution ranging from 5 to 150 Å, although coarser and finer grades are available. Advantages of powdered activated carbons are their lower processing costs and their flexibility in operation. The dosage of powdered activated carbon can be easily increased or decreased as process conditions vary. Powdered activated carbons are mainly used for liquid-phase adsorption. They are added to the liquid to be treated, mixed with the liquid and, after adsorption, are removed by sedimentation and filtration. Powdered activated carbons are generally used in batch process as the amount added can be easily altered and powder can be easily removed. The wet powder cake is not regenerated because of the problems associated with recycling the carbon, but incinerated or placed in landfills.
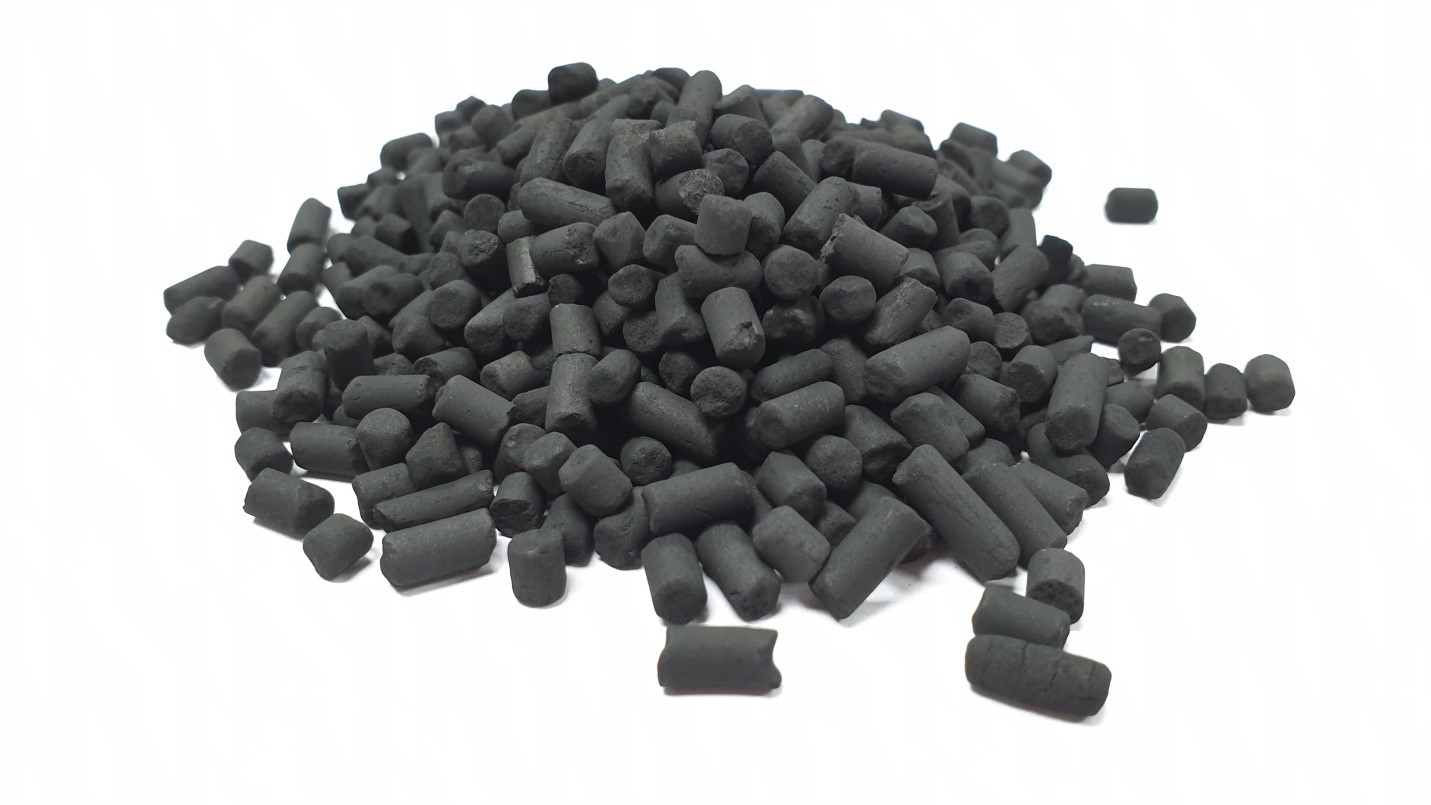
Extruded carbon
These are cylindrical pellets with diameter ranging from 1mm to 5mm. The extrusion process, together with the raw material used, ensures that the end product is hard and suitable for heavy duty applications. The extruded pellet form gives a low system pressure drop, which is an important consideration in the gas-phase uses. Markets lie in solvent recovery, gas purification and automotive emission control, where the high volume activity, low pressure drop and high stock resistance of extruded carbon enable them to last the entire life of the vehicle.
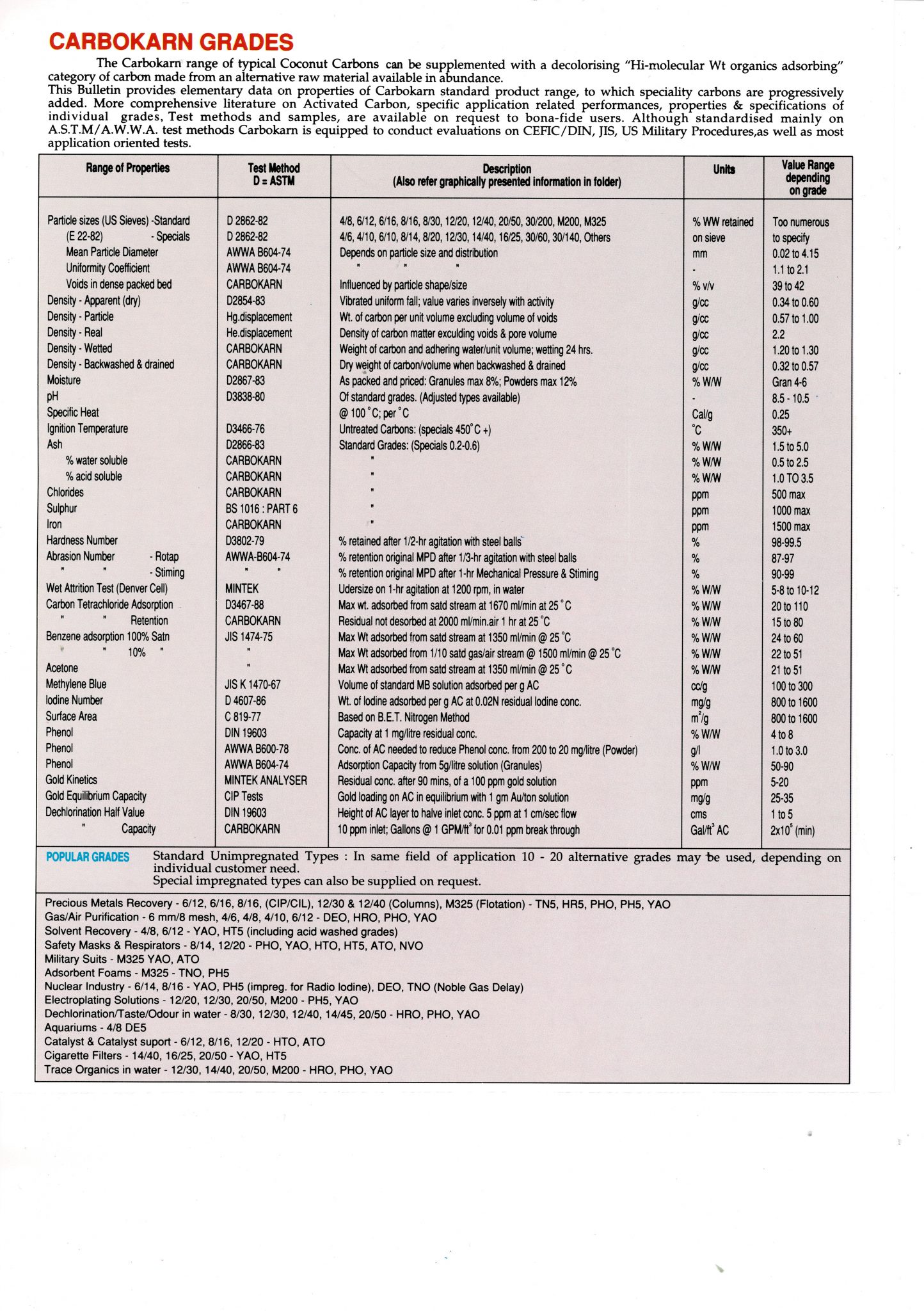